
Masks were the Common Thread
Masks.
The word that I will be happy to have leave my lips and my warehouse.
Now before anyone gets out of sorts, that is not a political statement. Far from it. We have been trying to educate the general community about the safety and efficacy of (our) masks, and encourage wearing them for the good of the public.
Of particular interest to us here at Wicked Sheets, is the usage of masks for those with sensitive respiratory systems or more specifically asthma and allergies. This is exactly why we thought the opportunity to share our asthma & allergy friendly™ certified fabric with the world in a new way was one that we had to seize.
Before I get ahead of myself, let us go back to the beginning: September 2020.
This is the month that changed our business as we know it. And yes, I know that COVID started in March.
As many of you know, before I started my “sweaty bedsheets company” in back in 2008, I was a verbal behavior therapist for children diagnosed along the Autism Spectrum. You can read more about that here. But the most important part of this story (and getting back to masks) is that when I “left” the field of Autism I vowed to figure out a way to impact the Autism community with my new venture.
Insert the Bluegrass Center for Autism (BCA).
In Louisville, Kentucky we were very limited in resources, schools, and therapeutic centers for those diagnosed along this spectrum. I began my career at Turning Point for Autism, which was then absorbed by the Home of the Innocents, and eventually the Autism Program was closed for restructuring. All of my old team members in those organizations (thankfully) stayed together and with a lot of passion, a lot of funding, and some amazingly driven parents, the Bluegrass Center for Autism was born. Beginning with one campus for the “young kids”, the center has grown to two campuses, a vocational training program, and a wait list that fills the moment it is opened to the public.
When I first began hiring team members for Wicked Sheets, one of the first places that I made the job posting was at BCA. I saw firsthand in the 27 or so families that I was privileged to be a part of during their child’s therapeutic journey, that it was very common for there to be a dichotomy between the parents. Generally, there was a stay-at-home caretaker and their counterpart was the rarely seen workaholic. And just to expound a bit, I use the term “workaholic” because whomever that parent was, their duty was to work and work as hard as they could. Someone has to pay for those therapy sessions and aides that the state will not cover.
Kentucky still has a "ways to go"
You see, in Kentucky at that time, and as is seen in some other states, Autism was not recognized as a medical condition and thus, insurance rarely would pay for any services. And traditional “therapy” was not intended for “our kids”. They needed this “crazy thing called operant conditioning that these old guys used to train pigeons and cats and rats”. Here comes my inner psychology professor, so I will get back to the point.
What you are left with then, are the resentful homemaker and the tired workaholic. It is already hard enough to just be happily married! Raise a kid or two and THEN add a diagnosis on top of it; the ground gets shakier than you can ever imagine.
How can I create change?
My thought: hire the stay-at-homes to work in the warehouse!
They (these parents) can work flexible day or nighttime hours while their child is at school, in therapy, have a sitter, or the spouse is home from work. We have a range of tasks that can and need to be done from fulfillment to marketing to deliveries to patchwork. I knew that I would always be able to find something.
Insert Maureen.
Her, then, 19-year-old son, V was one kiddo that I had met before when he was much younger, but I was never on his case. Maureen saw the job posting and had years of sewing experience and even had a degree in interior design. She and I hit it off upon our first meeting - even shared a few tears - and she was hired that afternoon. My plan was working. Little did I know, this realignment with BCA would lead me to face masks 3 years later.
Being that V was getting to an age where he would begin vocational training, Maureen mentioned to the supervisor, Bill, that we might have some work that “the guys” could do for us at Wicked Sheets: shredding, sorting, cleaning, etc.. Again…we will always be able to find something.
A few weeks later, Bill and his team came to check out our warehouse and facility. They deemed it a good fit and asked if they could bring a few guys out next week to start training. Since I had been in the field for so long, I knew that our warehouse had to be a good fit for their students not just for us. So, we went so far as to removing and/or hiding all the nuts, gluten, milk, etc., turning off any extra noises that we could control, making sure they all knew where the restroom was, and the most important of them all…making sure their (reward-providing) iPads could connect to the Wi-Fi. 😉
Set them up for success
To get our guys acquainted, Maureen thought like an #AutismMom and put together a few things that they could master easily and build confidence: sorting colors of fabric. Sorting grew into folding, then measuring and cutting, and we could even squeeze in some art projects, so long as I kept my Tootsie Pop stash stocked.
Before we knew it, it was March and they had sorted nearly 19 boxes of waste fabric for us. Never having manufactured in-house before, we did not realize what 5% waste looked like. And for those of you wondering why 5% waste means in manufacturing, it means that we use 95% of our (cooling) fabric when we create a bed sheet set (fitted, flat and two pillowcases) and the remaining 5% is wasted material; meaning it has no designated home. The goal at Wicked Sheets is to keep our waste percentage between 5-15%, which is solely dependent on the product created and how efficient we can be with our cutting and sewing. THIS is a hard metric to maintain and track.
Nonetheless, here we were with 5% waste staring us right in the face and now we needed a place or product to put it into. My team mentioned things here and there about what we could make, but I always made these decisions with my “cool, dry, better sleep lens” on. And believe me, it is tough to say now when you come up with a fantastic ideas (no sweat socks, neck pillows, bra liners), but on those days I practice being Katherine Heigl's character, Jane in the movie 27 Dresses.
Insert COVID-19.
Late in March, one of my Board members and I met to discuss the state of the business. There he mentioned that masks were going to be in high demand if COVID was not under control soon. Fortuitously, he asked if our fabric, already being certified, would be a good use for a mask. A few days before that we heard similar whispers on the radio in the warehouse and we thought about it then too. We were a bed sheet company after all and regardless of whether or not we had elastic, I just did not have the gut feeling…yet. And if you know any other entrepreneurs, you know that we like to trust our gut.
Then like every good story…my phone buzzed. It was a text from my dear friend and fellow entrepreneur, Tony Diebold. He owns and runs Fabricated Metals here in Louisville and his adorable wife is a fertility specialist that operates out of her own private practice. Like we heard from many other standalone facilities, private practices, and clinics, they were not given PPE early on. So, he, being the fantastic spouse and entrepreneur that he is called and asked if there was any way we could use our fabric and make masks out of it for his wife’s practice. Done and done.
Shortly thereafter we stopped manufacturing bedding and started making masks from our waste and what we call our “Frankenstein” elastic (little bits and pieces from the end of a roll). Finally, our waste AND our masks had a home!
Insert social media.
Little did I know, there were truly no other companies making masks yet or at least selling them on their websites yet. The date was April 1, 2020 and we had created a link for the families of the doctors and nurses who were donating to, to place their orders. I told my team that they could each have a priority list of 10 family members that we would send to first. We really did have a great plan. Until…Twitter got ahold of the link and we sold nearly 15,000 in 24 hours.
Great problem to have, except when you are in the middle of a rapidly spreading viral pandemic. No people, no shipping, no materials, no stores. Thanks to my quick thinking and tight knit team, we rallied together and arranged a group of volunteers to help us cut the pre-sorted fabric. We made patterns out of cardstock we had lying around. And I went to every store that was open and bought the sharpest scissors available.
At first, we had just friends and family helping us cut and our internal team of 3 was sewing around the clock. The problem was, however, that we never started with inventory. As soon as we had any finished masks completed, we shipped them to first responders, the US military, the county coroner’s offices, law offices, and a few pharmacies. Three in-house sewers were not going to cut it (pun intended!).
Call in the troops!
Through our network of volunteers and social media posts, we were able to get in touch with the Kentucky Museum of Arts and Culture (KMAC) and with a sewing consortium and fashion collaborative that Sarah Jane was a part of while she was living in Lexington. Before we knew it, we had hired 28 cutters and sewers from around the region. They were either working from home or coming in in shifts to our warehouse – which I cleaned religiously, and basically lived in for 3 months. My poor husband!
It took us a few weeks, surviving a global elastic shortage, shipping delays, 100’s of lost or stolen masks, and a few angry customers (some REALLY angry customers), but we made it. Our mask prototype went through 6 versions before we found one that worked and able to be replicated by our home sewers. And just for some consumer product relativity, creating and amending 6 versions of prototypes in consumer products typically takes months, sometimes years. My team did it in 36 hours.
The other heroes in our story
The 36 hours that I am referencing above did not simply include prototyping and testing. Without the swift responses from our legal team at Stites & Harbison, our fabric certifying body, Allergy Standards and the asthma & allergy friendly team, our web team at Louisville Geek, who managed our web traffic around the clock, and my Marco Polo crew listing to me sob after my 8th 14-hour shipping day in a row, we would not have made it.
Side note: When this is long gone, I will write another blog about the death threats that my friends and I received from customers. Yes, that really happened. On more than one occasion.
Time to wrap it up.
Today is January 22, 2021. It has been almost a year of dealing with this virus and we continue to make and sell masks daily. Here is the link to our best-selling mask, by the way. Good Housekeeping has promoted it on three separate occasions and is listed as the #1 Face Mask to workout in by The Manual. So, when I think back to how important those early decisions on our 6th version were, this is why. At Wicked Sheets, we never produce and release a product that does not meet our standards of quality, functionality, comfort, safety, or wicked goodness.
We have resumed manufacturing our bedding and sleep products. The team has grown by 4 people. The warehouse is a lot cleaner and more organized than it was back in the Spring. I am back to only working 5 days a week. And hopefully our mask marathon is over, for so many reasons.
To bring it back full circle, it all started with our promise to be a zero-waste facility and partner with the Bluegrass Center for Autism. At the time, we had no idea that these decisions would impact our business in the ways that they did. This community has given us a lot and for that we are so thankful.
Stay safe out there, friends.
-Alli
For more information about how to partner with the Bluegrass Center for Autism or how to be listed as an Autism-friendly business, email us at info@wickedsheets.com or check out their websites.
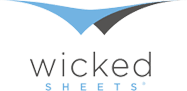
Wicked Sheets is a better sleep company, dedicated to providing products and information to deal with night sweats and hot flashes. Check out the rest of the site and our products to learn more.